Flat Die Pellet Mill Design Strategies for Successful Production in Plant
When it comes to efficient biomass pellet manufacturing, the flat die pellet mill design undoubtedly takes the lead. It embodies the perfect fusion of engineering craftsmanship, infusing pellet production with a whole new vitality. Its compact form and exceptional performance elevate pellet production efficiency to new heights. We commonly think of optimizing flat die pellet machine design can make productivity and efficiency of the pellet making machine improved. But many people do not understand how to achieve unparalleled profits by improving flat die pellet machinery design. So let's uncover it through this article.
Flat Die Pellet Mill Design in Business Plant
Demystifying Flat Die Pellet Mill Design: Types and Working Principles
For those who know about pelleting machines, they are no strangers to flat die pellet mills. Flat die pellet machine is a commonly used pelletizing equipment at cheaper prices, which can be divided into single roller flat die pellet machine and double roller flat die pellet machine according to the different structure and working principle. The working principle of flat die pellet mill is very easy to understand, which is to use rolling pressure and friction between the rollers to make the raw materials form a continuous compression, cutting and molding process between the rollers, and finally form the desired particles. Single roll flat die pellet maker presses the raw material into pellets through the squeezing action of the rollers while double roll flat die pellet maker squeezes the raw material into pellets through two relatively rotating rollers. However, how to maximize the business benefits by optimizing the design of the pellet maker machine has become a hot topic today. The following will reveal the secrets of the design of the flat die pellet mill for you. (Related to GEMCO Pellet Machine Price>>)
Double Roller Flat Die Pellet Mill Design and Working Principle
Mastering Flat Die Pellet Machinery Design: Essential Principles for Efficiency
When designing a flat die pellet mill, these basic principles should be taken into account to ensure that the flat die pelleting equipment can operate efficiently and stably and meet the expected pelletizing requirements. At the same time, the design can be further optimized and customized according to the special needs of specific applications and different costs. (Related to Page of GEMCO Products>>)
Pellets Made by Flat Die Pellet Maker Machinery for Sale
- Production Capacity and Power Calculation
Determine the production capacity requirements of the flat die pellet machinery, including the amount of raw material to be processed per hour and the amount of pellets to be produced. Also, estimate the electrical power required to ensure that the flat die pellet mill will be able to meet the expected production demands.
- Determination of Equipment Size and Weight
Consider the installation site and space constraints of the flat die pellet mill to determine its size and weight to allow for smooth installation and maintenance. The design also takes into account the stability of the equipment and ease of transportation.
- Influence of Feedstock Characteristics on Design
Understand the characteristics of the feedstock to be processed, including its pellet size distribution, moisture content, and viscosity. These characteristics will influence the design of the feed system and pelletizing machine structure to achieve an efficient pelletizing process.
- Satisfaction of Pellet Quality Requirement
According to the required pellet quality requirements, design the appropriate feeding system, extrusion device and screen structure to achieve the required pellet size and shape. Consideration should also be given to the homogeneity and stability of the pellets.
- Consideration of Operation Stability and Reliability
Consider the stability and reliability of the flat die pellet mill in long time operation. This includes the rationality of the equipment structure, wear resistance and the reduction of the failure rate. If necessary, suitable sensors and monitoring systems can be used to monitor the status of the equipment in real time.
- Cleaning and Maintenance Design Principles
Ensure that the flat die pelletizer machine is easy to clean and maintain, including components that are easy to disassemble and clean, as well as good maintenance instructions and care procedures. In addition, it is also important to consider the availability of wear parts and spare parts for the equipment.
- Safe and Environmentally Friendly Design
Consider the operational safety and environmental friendliness of the flat die pellet maker machine, including safety measures to protect the working environment, noise and dust control, and sustainability of waste disposal. Production must comply with relevant safety standards and environmental regulations.
Concern | Rating (1-10) |
---|---|
Production capacity and output | 9 |
Uniformity and quality of pellets | 8 |
Equipment price and cost | 7 |
Durability and lifespan of equipment | 8 |
Energy consumption and operating costs | 6 |
User-friendliness and maintenance | 9 |
Granulation process and technical support | 7 |
Equipment safety and compliance | 8 |
Footprint and layout of equipment | 6 |
Manufacturer's reputation and after-sales service | 9 |
Designing a High-Performance Flat Die Pellet Machine: Key Components and Excellent Construction
While following the basic principles, professional flat die pellet mill manufacturers are also focusing on the design of the machine's components and structure. Excellent design of components and structures plays a key role in the pellet production line. Therefore, if you want to buy flat die pelletizers to start your biomass pellet plant, you can ask the pelletizer supplier about the design of key components and structure to evaluate the performance of the pelletizer equipment.
Flat Die Pellet Machinery and Related Accessories Design and Structure
Design and Selection of Feeding System
The design and size of the feeding system takes into account the characteristics of the raw material and the production requirements. The design needs to determine the appropriate feeding method, such as gravity feeding, screw feeding or pneumatic conveying. At the same time, appropriate feeding equipment, such as vibrating feeder, screw conveyor or pneumatic conveying system, is selected to ensure that the raw materials can enter the flat die pellet mill in a stable and uniform manner.
Design and Selection of Pellet Extruder Equipment
Extrusion device is a crucial component in flat die pellet mill, which extrudes and deforms the raw material and forms pellets. The design of the pelletizer extruder should take into account the characteristics of the raw material, the pellet size requirements and the transfer of extrusion force. Common pelletizing extruder machines include rotary extruders, screw extruders and double extrusion rollers.
Design of Screen Structure and Screen Plate
The design of screen structure and screen plate plays an important role in particle separation and screening. The screen structure includes screen holder, screen frame and screen mesh. The design needs to consider the size and shape of the screen holes to meet the requirements of particle size, while ensuring the flow rate and screening efficiency. When you buy flat die pelletizer to setup a pellet production factory, you need to pay attention that the material selection and structural design of the screen panels also need to consider wear resistance and easy replacement.
Design of Cooling System and Control System
The cooling system is designed to rapidly cool and solidify the pellets to ensure stability and quality. Common cooling methods include natural cooling, airflow cooling and water cooling. The design needs to consider the temperature control and flow regulation of the cooling medium to meet the needs of different pellets.
The design of the control system mainly includes electrical control and automation control. Electrical control involves control panels, electrical components and software programming, etc., which are used to realize the functions of starting and stopping, monitoring and troubleshooting of operating parameters of the flat die pellet mill. The automation control can integrate sensors and feedback control system to realize the intelligent and automatic operation of the pellet line and improve the production efficiency and quality stability.
[Click here] Free Wood Pellet Machine Design PDF Download>>
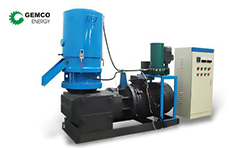
ZLSP Wood Pellet Machinery for Sale
This is a Flat Die Pellet Mill Operator's Guide PDF (Model ZLSP). Among them, ZLSP-420 biomass pellet mill (pictured on the left) is considered to be the most cost-effective biomass pellet maker machine among the GEMCO pelletizing machines.
In this wood pellet making machine guide, everything about two different structure types of flat die pelletizers (rotating die and rotating roller) is detailed. It certainly includes the flat die pellet mill structural design that you want. If you are interested in GEMCO wood pellet making machine, Please click on the link above to download the FREE pelletizer PDF. I hope this PDF is helpful to you.
If you want to know more about pellet mill design and structure, you can contact us to get a more detailed pellet machine design PDF or pellet machinery structure diagram. GEMCO ENERGY, as a professional biomass pellet mill manufacturer, can meet all requirements you have in terms of machine.