2TPH Wood Pellet Plant Project Setup in Australia
Wood pellets are the biofuels that are manufactured from sawdust or similar wood residues that can be easily obtained from the different industries. Depending on the purpose of use, wood pellets are used on the commercial as well as on a personal level. GEMCO provides customized plan for customers to easily setup complete wood pellet plant at low cost, including factory layout and process design, equipment selection, manufacturing, installation and commissioning and more. Welcomed to contact us to get more project report for your reference!
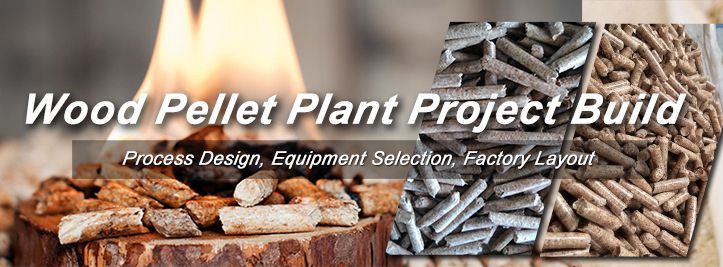
Setup Wood Pellet Plant Project
2T/H Wood Pellet Plant Project Setup in Australia
- Project Size: Geelong, Victoria, Australia
- Capacity: 2 Tons Per Day
- Raw Materials: Softwood (90%) and Hardwood (10%)
- Final Products: Wood Pellets
- Pelletizing Process: Crushing → Mixing → Pelletizing → Cooling → Elevating → Packing
- Main Equipment:
The 2T/H biomass wood pellet plant was built in Geelong, Victoria, Australia and successfully completed in 2012. The raw material was the mixture of softwood and hardwood, while softwood takes a proportion of 90%. The required production capacity was 1.5-2ton/h. The best moisture of such mixture should be 12%. The wood pellet production process of this project included crushing, mixing, pelletizing, cooling, elevating and packing. The packages were divided into 15kg per bag and 1ton per bag to meet different market demands. (See more: Successful Biomass Pellet Plant Project Built by GEMCO >>)
Below was the details of this wood pellet plant equipment onsite installation and commissioning by GEMCO professional technical support team.
Highlights of Australia Wood Pellet Plant Project
The remarkable feature of this wood pellet plant is that it adopts material mixing process, which realizes the stability of raw material entering pelletizing chamber and guarantees the continuous and stable running of equipments. Compared to those pelletizing equipments made in USA or Germany, our wood pelletizing machines can endure a high material moisture content of 13-15%, so that customer can greatly lower the energy input in drying process, thus decreasing production cost.
3D Diagram of Biomass Complete Projects
Besides, the electric circuit of this wood pellet plant strictly obeyed Australia/New Zealand electric standard. The plant was also equipped with emergency stop system and independent power switch for every single piece of equipment to assure operating safety.
Australia 2T/H Wood Pellet Plant Project Installation & Commissioning Video
2 ton per hour wood pellet plant in Australia – buy high quality wood pellet mill for biomass pellet making: hot sale wood pellet plant project offered by biomass pellet machine manufacturer or supplier, guide on process of wood pellet production and how to start wood pellet manufacturing business with limited cost in Tanzania, Egypt, Morocco, Ghana, South Korea, etc.
Commercial Wood Pellet Making Process
The wood pellet making process involves different steps that ensure the production of quality wood pellets. Want to learn how wood pellet production process works? We have divided the whole process into sequential steps. Let’s go through each step to make it more understandable for you!
Commercial Wood Pellet Production Process
- Selection of Raw Material
It is one of the most important steps. The raw material should have good quality. Its quantity depends on how many wood pellets you want to produce. If you are producing wood pellets for personal use, then you can use your farm waste to make pellets. If you want to make wood pellets on the commercial level or want to sell them in the market, then you can use wood waste obtained from numerous industries that supply wood residues. But this wood waste will not be enough if you have a large pellet production line and have to produce wood pellets in a very large amount. You will use wood or branches for large scale production of wood pellets.
- Processing of Raw Material
In the next step, raw material will be processed. It will go through the following stages:
- Sieving: If you doubt that your raw material will have contaminants like stone, plastic, or other particles then sieve the material to separate them.
- Grinding: Material will be ground so that it has a very fine size that is needed for the production of good quality pellets. Wood chippers are used for this purpose.
- Drying: Now the material will be dried so that extra water evaporates and only the needed amount is left behind. If raw material has more moisture content than the normal amount (8% to 10%), the wood pellets produced will not have high density and good quality. In this step, a dryer is used.
- Formation of Pellets
Now comes another crucial step. Biomass pellet mills are used in this step to manufacture wood pellets from the processed raw material. The material will be passed through the machine which will compress it and form pellets of different lengths and diameter. Two types of pellet mills can be used in this step. One is a ring die pellet mill which is mostly used for large scale production. The other one is a flat die pellet mill which is commonly used for small scale production. You can use any of these machines depending on your needs.
- Sieving and Packaging
Before packing the newly formed pellets, they are sieved to separate the fine particles from the pellets. Once a high-quality product is achieved, it is packed into containers or packets so that environmental factors like moisture, etc. do not have any effect on the pellets. (Related machine: Pellet Packing Machine >>)
Characteristics And Uses Of Biomass Wood Pellet Fuel
The main purpose of its biomass wood pellet machine is to process wood chips into pellets that can be used as fuel. Whether it is widely used depends on how we use it. Waste wood chips and wood scraps from wood factories and furniture factories can be processed into wood pellets, turning waste into treasure. The density of the pellets after molding is greater than 1100kg/m3, which improves the transportation and storage capacity of biomass materials, improves the combustion performance, and improves Utilization efficiency, and reduces the production of harmful substances after burning.
Amount of heating generation (lower limit) | 4.7 kWh/kg = about4,000 kcal/kg |
---|---|
Kerosene conversion value | pellet:kerosene = about2.1tons:1m3 |
Volume weight | 650 kg/m3 |
Hydrous rate | 8-13% |
Ash | wood except bark: under 0.5%, bark: over 2.5% |
- Small boiler: Mainly used for household heating and supply of domestic hot water. This kind of application is mainly based on biomass pellet fuel. This kind of product is miniaturized, easy to produce in assembly line, single product is beautiful and generous, and suitable for household use.
- The unprocessed biomass fuel is directly burned. Most of these are small and medium-sized boilers. Since the fuel is not processed, investment costs can be saved. This type of boiler fuel is mainly industrial waste, because it uses its own waste to generate steam or heat, which greatly saves the investment in other fuels and the previous waste treatment expenses, and enterprises are very enthusiastic about application.
- The raw materials are rough processed, and then directly burned to generate electricity or steam. For example, break the straw, break the wood blocks and wood strips, and then send them into the combustion chamber by a conveyor (pneumatic conveying or mechanical conveying). This type of application requires that the plant be built near the source of raw materials to reduce transportation costs.
Using Wood Waste to Make the Pellets
In addition to wood chips, agricultural and forestry residues such as straw, rice husk, and bark are all raw materials for biomass pellet machines. Biomass fuel pellets have great energy utilization potential and market prospects. Therefore, the establishment of a biomass pellet processing plant can not only provide more incentives and support for fuel pellets, but also be a profitable commercial project.If you want to buy complete biomass pellet processing equipment, please contact us, The pellet making machine produced by our company has the characteristics of unique design, reasonable structure, high efficiency in energy reduction, and long life. We hope that we can make your pellet production business more smoothly.
- Hello team, we are in Dar es Salaam, Tanzania, and we are interested in investing in the wood pellet processing industry. We are also interested in your pellet making machine. Please briefly describe to us how long the service life of the ring die of the sawdust pellet machine is. Does it need to be updated frequently?
- The service life of the ring die of the pellet machine is usually calculated by the quality of the processed material. The life of the ring die of general quality is about 800-1200 hours, and the life of the ring die of good quality is about 1500-1800 hours. There are certain reasons for this and the cost of the equipment.When the ring die is not in use, squeeze out the remaining raw material to prevent the heat of the ring die from drying and hardening the material remaining in the die hole, resulting in no discharge or cracking of the ring die, reducing the service life of the ring die. GEMCO machinery can design and customize ring molds of different processes in accordance with the different raw materials and actual use conditions, so as to ensure that the ring molds can play their due value.