Feed Batching Process: Vital Element in Animal Feed Business Plans
In modern farming, feed quality has a direct impact on animal health and productivity, and the feed batching process is at the heart of shaping great feed products. Whether you are a novice or a seasoned expert, a deeper understanding of the feed proportioning process will open the door to success. This article is designed to explore the animal feed batching technology and equipment used in the batching section of the animal feed processing industry, presenting innovative batching methods, advanced batching machinery, and necessary considerations for your feed pellet plant construction. Hopefully, this article will help your animal feed business plan succeed. (Link to The Relationship Between Crushing Process and Dosing Process>>)
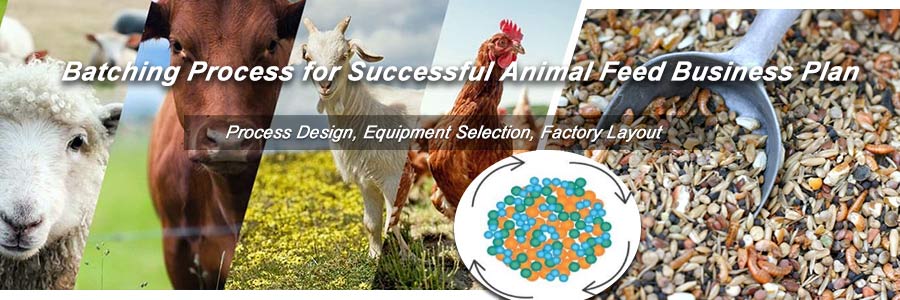
Batching Systems in Animal Feed Business plan
Ingredient Dosing Specifications in Animal Feed Business Plans: Meeting Quality Standards
How to run a successful animal feed production business plan? The first step is to figure out the requirements of the batching process when processing animal feed and how to meet the feed batching requirements.
Ingredient Dosing Criteria in Batching Systems: Elevating Feed Standards
In a successful animal feed making business, the dosage system ensures that the product is accurately proportioned by accurately measuring each feed ingredient. In short, a proportioning system should meet the requirements of accurate, reliable and efficient dosing.
- Controlling Proportioning Error Margins Within 0.1%:
Animal feed mills are required to achieve precise ratios to ensure nutritional balance and quality consistency from batch to batch. According to the animal feed formula, the proportioning error should not exceed 0.1%.
- Achieving Over 95% Mixing Uniformity:
Mixing uniformity of raw material for making feed pellets is required to ensure that different feedstocks are fully mixed to avoid localized over or under-dosing.
- Automated Processes Surpassing 80%:
Animal feed manufacturing plants can achieve precise batching and automated production processes by using advanced batching control systems and batching devices to improve fully automatic animal feed plant efficiency and reduce human error.
- Managing Ingredient Blending Time Within 15-20 mins:
Animal feed processing plants should control the batching time of each batch to ensure that the batching target is achieved in the shortest possible time in order to improve feed production efficiency and reduce animal feed plant costs.
- Maintaining Hygiene Standards for Raw Materials:
For example, dust levels should be controlled below 5mg/m³ to ensure hygiene and safety in animal feed production. For a successful animal feed business plan, animal feed production manufacturers must follow strict laws and regulations and related rules.
Electronic Batching Scale in Batching Processes: Optimizing Proportioning Accuracy
Electronic batching scale is one of the key batching equipment in animal feed production, which is mainly composed of a load receiver (weighing hopper), connecting parts, load cell, control system (computer, PLC module, etc.), weighing display system and printing device. There are many advantages of electronic dosage scale in ingredient batching systems:
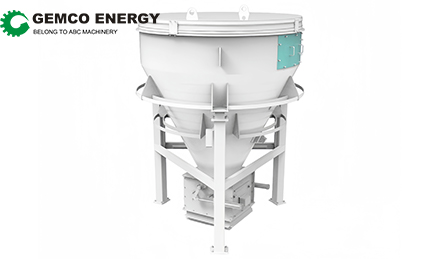
Gemco Electronic Batching Scale for Sale
Best Electronic Dosing Scale Performance | |
---|---|
Fast weighing speed | Small size and simple structure |
High accuracy and precision | High level of automation |
Good sealing of load cell | Easy to use and maintain |
High environmental adaptability | Long service life |
- Accuracy and Precision: Electronic dosage scales typically weigh and measure raw materials within a tolerance of 0.1% to 0.01%.
- Invariance and Stability: Electronic dosing scales typically have a stable service life of several years. They remain within 0.05% error under varying temperature and humidity conditions.
- Capacity and Range: The capacity range of the electronic scale should be able to weigh different sizes of raw materials from a few grams to several tons.
- Ease of Operation and Automation: The operator interface should be simple and intuitive, and should be able to be integrated with other Automatic feed production machines to increase animal feed companies' productivity by at least 20%.
- Durability and Ease of Cleaning: The electric weigh scale should be durable, able to withstand 24/7 continuous use and be dust and water-resistant. Easy cleaning ensures hygiene and avoids cross-contamination. Cleaning time should be limited to less than 30 minutes after each batch.
If you are interested in electronic batching scales, you can contact us directly for a free consultation and the latest quotation!
Effective Proportioning Process for Animal Feed Business Plan Blueprint
In the animal feed production line, the design of a reasonable animal feed dosing process flow lies in the selection of the correct specifications and quantity of feed dosing and measuring devices, and making it fully coordinated with the dosing and feeding equipment, mixers and other equipment. The common batching process in industrial feed mills has several forms such as one bin one scale, multiple bins one scale and multiple bins several scales (2~4 batching scales).
Actual Ingredient Batching System in Animal Feed Business Plant
Single-Bin and Single-Scale Ingredient Batching Process
The one-bin and one-scale batching process is applied in small-scale animal feed processing units with 8 to 10 ingredient bins, each equipped with a weighing scale underneath. Every scale may have varying capacities. During the working process, each scale independently completes the ingredient cycle of feeding, weighing, and discharging. This feed ingredient processing method is now less commonly used.
- Advantages: Shorter ingredient cycles and higher proportioning accuracy.
- Disadvantages: requiring for multiple weighing equipment, higher batching scale investment cost, and complexity in maintenance and operation.
Multi-Bin and Single-Scale Ingredient Batching Technique
Multi-bin-one-scales process is used in small feed processing plants with 6 to 10 batching bins. The animal feed processing line is only equipped with one electronic dosage scale. Each batching silo weighs the ingredients in turn. This dosage process is currently less used.
- Advantages: For some small feed mills or mini feed mills, this batching process is also a good choice because of simple operation, low investment in equipment, easy maintenance and easy automation.
- Disadvantages: Batching cycle is relatively long reducing production efficiency. Small proportion of raw materials (5% to 20%) in the weighing error is very large reducing feed quality and increasing animal feed production costs.
Multi-Bin and Multi-Scale Ingredient Batching Method
The more widely used feed batching processes in commercial feed mills are multi-bin-dual-scales and multi-bin-triple-scales. In the dosage process, the feeder machine will send the raw materials to the weighing hopper in sequence. Raw materials with large ratios (≥20%) are sent to the large hopper, while raw materials with small ratios (5%-20%) are sent to the small hopper for weighing. The dosing of each kind of raw material is controlled by the dosage controller device to feed the feeder device, i.e. it is realized by the switch of the feeder according to the set sequence and time.
When all the materials in the silo are weighed and dosed according to the set feed formula and reach the specified cumulative weight (per batch), the weighing hopper door opens, and the materials in the weighing hopper are put into the animal feed mixing machine for mixing, and the animal feed mixer machine opens the unloading door to unload the materials into the buffer bin to wait for the next process in the feed production line when the predefined mixing time, i.e., the mixing machine homogeneity reaches the requirement.
- Advantages: proportioning a wide range of raw materials accurately and quickly; reducing proportioning errors; improving feed plant production efficiency and product quality; reducing animal feed mill costs with accurate dosing capability and automated operation; ensuring a hygienic and safe production environment. Therefore, modern animal feed mills mostly use this batching process.
GEMCO Solutions: Contributing to Animal Feed Business Plan Success!
Selecting the best batching equipment is a critical part of a successful feed mill business. The dosing system needs to consider the animal feed plant layout, production capacity, investment, and other factors to ensure an efficient feed mill process. Therefore, it is crucial to invest in advanced dosing systems and choose excellent dosing equipment in animal feed mill production. (Read more about Animal Feed Mill Processes and Machines>>)
GEMCO provides turn key solutions for animal feed mill services and is committed to customizing batching systems and batching machinery for you. With advanced technology and rich experience, we can design the animal feed production line according to customer's needs and provide you with a personalized animal feed manufacturing business plan PDF. Contact us now, and let us together on the road to successful animal feed manufacturing.