Raw Material Reception: First Step to Animal Feed Plant Profitability
Raw Material reception is the first process of poultry feed plant production and an important process to ensure production continuity and product quality. From the source to the plant, each step is critical. Well-designed raw material receiving procedure and modern equipment help to ensure raw material quality and safety. In this article, we will look at the key considerations for animal feed ingredient receiving and the associated processes and equipment to ensure the successful implementation of your animal feed mill business plan and the efficient operation of your animal feed pellet production line.
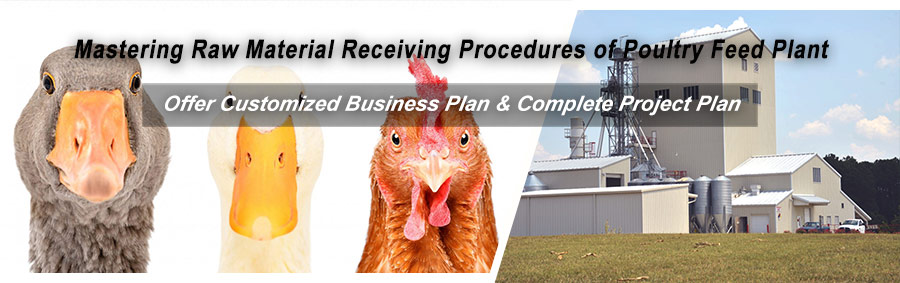
Raw Material Receiving Procedures of Animal Feed Pellet Plant
Precision Management of Material Receiving: Essential Attention Points
Receiving raw material is not as simple as it seems, and the process involves several key points. Poor quality raw material for feed mill production can damage poultry feed processing machinery, increase maintenance costs, and lead to reduced poultry feed production line capacity and finished feed quality issues. This ultimately increases the overall cost of poultry feed mill plant processing and has a direct impact on the profitability of the business.

Animal Feed Raw Materials in Poultry Feed Plant
Crucial Task in Raw Material Receiving for Animal Feed Manufacturing
The task of receiving raw materials is to feed the various raw materials required by the animal feed production plant through certain procedures, storage or directly into the animal feed production line to use. The raw material receiving capacity of the animal feed factory must meet the needs of the production capacity of the production line. Through using advanced technology and equipment, it can ensure the timely receipt of raw materials, reduce the labor intensity of employees, save energy consumption, reduce poultry feed plant production costs, and also help to protect the environment.
Essential Requirements for Raw Material Reception in Poultry Feed Plant
The production of quality animal feed begins with the reception of raw materials, so it's important to control the raw material receiving procedure strictly. This is not only to ensure the safety of the final animal feed product, but also to minimize the wear and tear of the animal feed processing equipment on the manufacturing line as well as to reduce unnecessary plant operating costs.
- Equipment Reception Capacity
The receiving capacity of the animal feed mill equipment needs to meet 3~5 times of the feed mill's production capacity in order to cope with large-scale production demand.
- Consideration of Raw Material Diversity
Animal feed mills need to consider the differences in morphology, physical and chemical properties of different raw materials, as well as different packaging forms such as bulk, bags, bottles, cans and so on.
- Stringent Standards and Inspection
In addition to purchasing raw materials according to the local raw material procurement standards, the poultry feed mill plant should also select experienced quality inspectors to inspect the feedstuffs to be received. It is necessary to strictly grasp the raw material acceptance barrier to prohibit unqualified raw materials into the poultry feed production line.
- Detailed Verification Procedures
Poultry feed plants carefully check the incoming raw materials to ensure that the packaging is intact. Labeling information such as feedstuffs name, brand, content, packaging, packaging integrity, labeling, production date, shelf life, and other accurate and complete. In addition, animal feed milling plant should observe the color, foreign matter, particle size, odor, and other characteristics, and compare with standard products to confirm.
- Sample Collection and Testing
The poultry feed processing plant need collects representative samples and specifies testing items to ensure that the raw materials meet the requirements of animal feed product quality. Safety assessment, nutritional testing, and other special requirements if necessary.
- Comprehensive Testing and Evaluation
For new and unfamiliar feed ingredients, especially additives and other pharmaceutical ingredients, animal feeding tests are performed to confirm appropriate dosage, palatability and processability. In addition, other biological tests are performed to assess the impact on animal health, performance of feed processing machines, etc.
Contact us for free information about the impact of feed ingredients on the operation of your animal feed production line, and the impact of substandard raw materials on your plant's animal feed making machines. We provide professional answers and the best solutions for poultry feed production, ensuring that your poultry feed production line runs smoothly and your poultry feed pellet product quality is reliable.
Efficient Material Receiving Processes:Equipment Choices and Workflow
Next, I will start by describing the raw material receiving procedure of poultry feed plant. Then I will introduce the considerations and equipment used for land receiving, water receiving and liquid receiving respectively. Poultry feed plants according to the specific circumstances to choose the appropriate way to receive raw materials to reduce the cost of poultry pellet feed plant production.
Common Standard Operating Procedure for Receiving Raw Materials
Receipt of Raw Materials by Land at Animal Feed Mill Plant
Poultry feed plants receiving raw materials by land are divided into bulk and bagged two ways. Both receiving methods have a direct impact on the the animal food processing plant operation. Regardless of the method, it is a key step to ensure product quality and production efficiency.
- Methods for Receiving Bulk Raw Materials in Poultry Feed Mill Processing
Raw materials in bulk are mainly various grains and their processing by-products, which are weighed in the weighing scale and dumped into the receiving pit. In order to ensure safety, the receiving pit is equipped with a grid screen, whose aperture is generally 40mm × 40mm, which can not only protect the safety of workers, but also filter out the larger impurities in the raw materials. After the raw material enters the receiving pit, it passes through the horizontal conveyor, bucket elevator, primary clearing screen and magnetic separator, and finally transported to the vertical silo for storage, or sent to the bin to be crushed or batching bin.
- Methods for Receiving Bagged Raw Materials in Feed Mill Plant Processing
There are two ways to receive bagged raw materials: manual receiving and mechanical receiving. Manual receiving refers to the reliance on human transportation, usually high-cost but low efficiency. Mechanical receiving is the use of vehicles and other transport vehicles to transport bagged raw materials to the factory, and then manually move it to the belt conveyor, and into the warehouse. Mechanical receiving is highly efficient and low labor-intensive, but requires a larger investment in equipment.
Receipt of Raw Materials by Water at Animal Feed Manufacturing Plant
Pneumatic conveying is used in poultry feed mills to receive raw materials from waterways. The pneumatic conveying system consists of components such as suction nozzle, conveying pipe, unloader, valve, dust collector and fan. Under the negative pressure of the fan, the suction nozzle sucks the raw material from the cabin and sends it to the unloader through the conveying pipeline, and the separated material is sent to the storage bin through the subsequent conveying device. A pneumatic conveying system can be divided into mobile and fixed two kinds. Usually, large poultry feed mill plants tend to use the fixed pneumatic conveying system, while small feed mill plants can choose the mobile pneumatic conveying system.
Reception of Liquid Raw Materials at Animal Feed Processing Plant
According to the poultry feed formulation demand, the liquid feed ingredients required by poultry feed processing plants include fats and oils, molasses, liquid choline and liquid methionine. These liquid ingredients usually enter the poultry feed manufacturing plants in tanks or drums. After being weighed, they are pumped into storage tanks via receiving pumps, with pipelines equipped with filtration and de-watering devices where necessary. Fats and oils play an important part in the animal feed formulation and require special attention. Generally, animal fats have a melting point between 29°C to 48°C (84.2°F~118.4°F) and a flash point between 160 ~ 260 degrees Celsius (608 degrees Fahrenheit to 852 degrees Fahrenheit). If the flash point temperature is below 150 degrees Celsius (302 degrees Fahrenheit), the poultry feed production mill should stop receiving such fats immediately.
GEMCO: Manufacturing Expert Feed Machinery for Your Success!
If you have any needs, you can contact us directly to get a free consultation. We can not only provide you with poultry feed plant layout and design but also advise you about the poultry pellet feed machine required to meet your needs. We are committed to providing professional guidance and optimal solutions for your poultry feed production!
GEMCO, as a poultry feed machine manufacturer with nearly 30 years of experience, has exported animal feed processing machines and complete feed mill plants to many countries around the world, such as the Philippines, Chile, Uzbekistan, Nigeria, Tanzania, Uganda, Fiji, Russia, Kenya, etc., and has received unanimous praise. Contact us to start a successful journey in feed production!