Feed Storage Process: Strategies for Animal Food Processing Plants
Storage management in animal food processing plants is a key aspect of ensuring product quality and production efficiency. The correct feed storage method not only affects the freshness of raw materials and the nutritional value of feed, but also directly affects the production cost of animal feed mills and the market competitiveness of animal food. This article will provide an in-depth look at how animal feeds and their raw materials are stored in animal food processing plants, providing a practical guide for feed processing plant investors to ensure optimum levels of productivity and product quality.
Animal Feed Storage Process in Food Manufacturing Plant
Feed Mill Setup: Considerations for Animal Raw Material and Feed Storage Containers
The storage of raw materials and finished products affects the normal animal feed mill processing and the economic benefits. Silo type and capacity are the key factors to ensure that the quality of raw materials (finished products) storage, storage capacity, so when selecting, they all should be considered:
- Choose the warehouse type according to the stored materials characteristics and regional characteristics to achieve economical and reasonable results.
- Calculate the warehouse capacity and number based on the output, variety, and quantity of raw materials and finished products.
- Reasonably configure the location of the storage silo to facilitate management and prevent mixing, contamination, etc.
How to Choose Raw Material Storage Silo for Animal Feed Processing Plants?
Warehouse Type | Advantages | Disadvantages | Application |
---|---|---|---|
Room-Type Warehouses | Low construction cost; easy to build | Low mechanization level for loading and unloading; difficult operation and management | Suitable for powder, oil cakes and packaging materials, etc. |
Vertical Warehouses | Easy mechanization for loading and unloading; convenient operation and management; less labor required | High construction cost; high technical requirements | Suitable for storing granular materials such as grains |
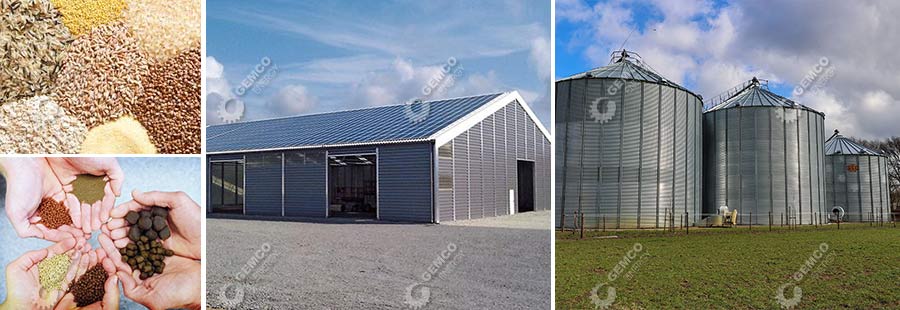
Classification of Feed Storage Silos in Animal Feed Processing Mills
The raw materials and finished feed in animal feed processing plants are many varieties and have different characteristics. If you have enough money to start your feed manufacturing mill, you can choose the combination of vertical warehouses and room-type warehouses. If you are capital-strapped or want to build a feed material storage system with minimum cost, you can consult us by clicking the button below. We will provide you with free advice based on your specific needs and funds.
Key Raw Material Storage Methods for Animal Food Processing plants
After animal food processing plants receive (Feed Raw Material Reception Procedure), feed raw materials need a certain time of storage before the normal feed manufacturing process. Storage technology to avoid feed spoilage, product loss, and biological attack is an effective means to reduce feed mill costs and achieve feed mill profitability. (Know more Animal Feed Production Process>>)
Methods for Storing Grain Ingredients in Animal Feed Factory
Cereal (Grain) Material is the most important ingredient of processed feed in animal feed mills. The key to its storage method is to prevent moisture, insects and mould. A well-ventilated warehouse with moderate temperature is usually used to avoid high humidity. The use of sealed containers or vacuum packaging is also an effective means of preventing moisture. For large-scale storage, the use of metal silos may be considered.
Methods for Storing Liquid Ingredients in Animal Feed Production Plant
In feed processing plants, liquid feed ingredients often used include grease, molasses, liquid choline, liquid, methionine, etc., of which grease and molasses are most commonly used.
- Oil and Grease Storage Methods
The oil and grease received in animal feed production plants include two kinds of plant oils and animal oils. Moisture is a major contributor to sour sludge and wear in fat storage tanks. All vegetable oils (fats) contain small amounts of foreign matter such as broken bones, hair, metal and other dirt. They accumulate at the bottom of the tank to form acid sludge, which can lead to clogging of screens and injector nozzles. Therefore, oil tanks should be cleaned at least every 6 months. This helps to maintain the quality of the grease and prevents clogging of the equipment, ensuring proper animal feed mill production.
- Molasses Storage Methods
Feed factories usually choose steel, concrete, or wooden storage tanks for storing molasses. It is common for feed manufacturers to choose either monolithic poured concrete or steel tanks for storing molasses. Molasses storage tanks should be properly vented. The tightness of the inlet lid needs to be adjusted to ensure air circulation while preventing dust or rainwater from entering the tank. In cold regions, molasses storage tanks are either wrapped with insulation materials on the outside or placed underground. At the same time, it is important to control the temperature of heated molasses to not exceed 46 ℃. Otherwise, it may lead to gelatinization and carbonization problems.
Methods for Storing Medications and Trace Elements in Animal Feed Manufacturing Mill
Drugs and trace elements require a high level of storage environment, which usually requires the use of cool, dry, and light-proof warehouses. Hermetically sealed packaging is the best way to ensure the stability of drugs and trace elements while avoiding mixing with other chemicals.
Animal feed ingredients storage methods and warehouse requirements may vary.For more information, please feel free to contact us.
Optimizing Finished Feed Storage in Animal Food Processing Plants
Whether it's bulk feed storage or whole feed storage, building a finished feed warehouse for a food manufacturing plant requires meticulous attention to detail. The following are basic considerations:
Interior view of the Animal Food Storage Silo Structure
- Ensure that the building structure is moisture and water-resistant. Choose terrazzo flooring to maintain a level surface and enhance durability.
- Prioritize effective ceiling insulation to regulate internal temperatures efficiently.
- The minimum height of the storage warehouse should be 4m, preferably between 6.5~8m to facilitate truck access.
- Allocate specific storage locations for each product category.
- Select shaded areas (cooler side) for optimum temperature control.
GEMCO’s Animal Feed Engineering Solutions: Professional Team Empowering Success
Every step in the process of setting up an animal food processing plant is critical and requires professional help and guidance. If you need advice and support from mechanical engineers and technical experts, contact us now!
Our company offers a full range of solutions for animal feed engineering projects. From project planning to equipment selection, to every aspect of production and operation, we can provide you with the best quality service. By choosing GEMCO, you can not only get high-quality animal food making machines and technical support, but also get the whole tracking service from our professional team to ensure the smooth completion and long-term success of your animal feed plant project.
Complete Animal Food Processing Line for Sale
Contact us now to get more information for free!